Hardware Washers: Types, Uses, and Maintenance Guide
Hardware washers, essential components in mechanical and construction applications, evenly distribut…….
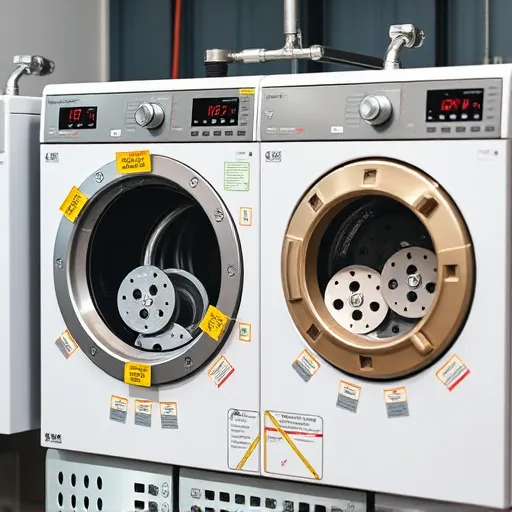
Hardware washers, essential components in mechanical and construction applications, evenly distribute pressure, preventing surface damage. With various sizes and materials (steel, plastic, brass) they enhance structural stability. Types include flat, spring, lock, and fender washers, each with specific benefits. Material selection is critical for longevity; carbon steel requires rust protection, while stainless steel resists corrosion. Proper installation and alignment prevent damage. Regular maintenance, including replacement and inspections, ensures optimal performance and longevity.
Flat washers, essential components in fastening systems, distribute load and prevent screw head strip-out. This article offers a comprehensive guide to understanding these versatile hardware washers. We explore various types, from lock washers to spring washers, highlighting their unique applications. Delving into material choices, installation best practices, common issues, and maintenance tips ensures optimal performance in diverse settings. Discover the crucial role of flat washers in everything from automotive repairs to construction projects, enhancing reliability and longevity.
- Understanding Flat Washers: A Basic Overview
- Types of Hardware Washers and Their Applications
- The Role of Washers in Fastening Systems
- Material Considerations for Flat Washers
- Installation and Usage Best Practices
- Common Issues and Maintenance Tips
Understanding Flat Washers: A Basic Overview
Flat washers, also known as hardware washers, are thin, flat rings made of metal or plastic used to distribute pressure evenly across a fastening point. They’re an essential component in many mechanical and construction applications, serving as a buffer between a bolt or screw head and the surface it’s attached to. This simple yet effective design prevents damage to the surface, ensures tighter joint integrity, and enhances overall stability.
These washers come in various sizes and materials, with each type tailored for specific uses. From standard steel washers that offer durability and corrosion resistance to plastic varieties ideal for preventing strippage and providing a low-friction surface, there’s a flat washer designed for almost every fastening scenario. Understanding their purpose and availability ensures efficient problem-solving and enhanced structural integrity in various projects, making them a fundamental part of any hardware supply.
Types of Hardware Washers and Their Applications
Hardware washers come in various types, each with unique characteristics and applications. One common type is the flat washer, a simple yet versatile component often used to distribute pressure evenly when joining two objects. Its disc-like shape allows it to fit snugly between bolts or screws and a surface, preventing damage caused by over-tightening.
Another variety is the spring washer, designed with a coiled spring mechanism that provides tension and prevents nuts from loosening. These are particularly useful in high-vibration environments like automotive or industrial settings. In contrast, lock washers offer enhanced security by biting into the bolt thread, preventing rotation and ensuring tighter connections. They are commonly employed in applications demanding superior fastener hold, such as heavy machinery construction.
The Role of Washers in Fastening Systems
Hardware washers play a critical role in fastening systems, ensuring that screws and bolts secure objects firmly together. They are designed to distribute the load evenly across a larger surface area, preventing damage to the material being joined. By acting as a spacer and bearing surface, washers prevent head or thread stripping, especially when working with thin materials. This simple yet effective component is essential for creating robust and long-lasting connections in various applications, from construction to automotive repairs.
In fastening systems, different types of washers are used depending on the material, load requirements, and environmental conditions. Common varieties include fender washers, lock washers, and split washers, each offering unique benefits. For instance, lock washers provide additional security by preventing screw head loosening due to vibration, while split washers allow for easy installation and removal, making them ideal for specific assembly processes.
Material Considerations for Flat Washers
When considering flat washers, material is a key factor. Hardware washers are typically made from various metals like carbon steel, stainless steel, or even brass, each offering unique properties. Carbon steel washers are cost-effective and suitable for general applications, but they may be prone to rust if not properly coated or used in dry environments. Stainless steel washers, on the other hand, excel in corrosive environments due to their resistance to rust and oxidation. Brass washers provide excellent conductivity and durability, making them ideal for electrical and plumbing applications.
The choice of material directly impacts the washer’s longevity, performance, and compatibility with specific tasks or settings. Flat washers made from high-quality materials ensure smooth operations, prevent damage to bolts and nuts, and maintain consistent tension in fastening systems. Understanding these material considerations is essential when selecting hardware washers for different projects to ensure optimal results.
Installation and Usage Best Practices
When installing flat washers, a common type of hardware washer used for fastening and sealing, it’s crucial to align them correctly with the bolt or screw. Misalignment can lead to damage or misfit. Start by ensuring the washer is level and properly seated under the head of the bolt. Tighten securely, but be mindful not to overtighten, as this could deform the washer or cause damage to the fastened components.
For optimal performance, flat washers should be chosen based on the specific application. For instance, for applications requiring high pressure or load, thicker washers may be necessary. Always consider the material of the washer, especially in environments prone to corrosion, opting for materials like stainless steel or coated varieties to ensure longevity and prevent damage from rust. Using the correct hardware washer type can significantly impact the durability and functionality of your assembly.
Common Issues and Maintenance Tips
Hardware washers, like any mechanical component, come with their share of common issues. One frequent problem is washer fatigue, leading to wear and tear, especially in high-pressure washing systems. This can result in leaks or even failure of the entire unit. Regular maintenance is key to preventing such issues. Replace flat washers periodically, as they are a relatively inexpensive part that plays a crucial role in maintaining water tightness.
To keep your hardware washers in top condition, ensure proper installation and tightening. Over-tightening can damage the washer or the threaded component, so always follow manufacturer guidelines. Additionally, periodic inspections for signs of corrosion or damage should be conducted. Cleaning the washers regularly can prevent buildup that might affect their functionality. Keeping these simple maintenance tips in mind will extend the life of your hardware washers and ensure efficient performance.
Flat washers, or hardware washers, are essential components in fastening systems, providing a crucial layer of protection between bolts and surfaces. By understanding their types, applications, and material considerations, you can ensure optimal performance and longevity in various projects. Proper installation and usage best practices, along with regular maintenance, will help prevent common issues, making flat washers reliable game-changers for many industrial and DIY tasks.