Hardware Washers: Unveiling Inner Diameters for Mechanical Excellence
Hardware washers are integral mechanical components vital for maintaining spacing, alignment, and st…….
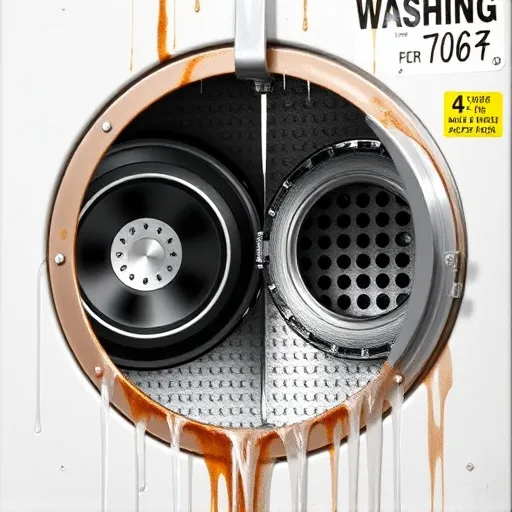
Hardware washers are integral mechanical components vital for maintaining spacing, alignment, and structural integrity in diverse industries, from automotive to electronics. Crafted from durable materials like steel or brass, these washers distribute loads evenly, prevent damage to sensitive parts, and accommodate misalignments. Inner diameters, subject to meticulous consideration, directly influence their effectiveness in supporting and protecting crucial mechanical joints. Their versatility is showcased by various types – spring, lock, and plain washers – catering to specific needs in automotive, machinery, construction, and electronics assembly. Choosing the right materials and precise dimensions for hardware washers ensures longevity, enhances performance, and promotes safety across a wide range of applications.
Hardware washers, a fundamental component in mechanical systems, play a crucial role in ensuring smooth operation and longevity. This article delves into the intricate world of inner diameters, exploring their significance within the context of hardware washers. We’ll unravel the basics of washer functionality, their diverse applications, and design factors for optimal performance. Furthermore, safety and reliability through proper washer selection will be highlighted, providing valuable insights for professionals in various industries.
- Understanding Hardware Washers: A Foundation for Inner Diameters
- The Role of Washers in Mechanical Systems
- Uncovering the Significance of Inner Diameters
- Types and Applications of Hardware Washers
- Design Considerations for Optimal Performance
- Ensuring Safety and Reliability Through Washer Selection
Understanding Hardware Washers: A Foundation for Inner Diameters
Hardware washers are essential components in any mechanical or automotive system, serving as a critical foundation for understanding inner diameters. These washers, typically made from durable materials like steel or brass, play a pivotal role in maintaining proper spacing and alignment between components. By ensuring consistent contact and load distribution, hardware washers prevent damage to sensitive parts, particularly when under stress or pressure.
Inner diameters, therefore, are not merely abstract measurements but must be carefully considered within the context of these washer mechanisms. The dimensions of hardware washers influence how effectively they can support and protect crucial mechanical joints, thereby dictating the overall performance and longevity of connected systems. Understanding this relationship is key to optimizing designs and ensuring robust functionality in various applications, from automotive repairs to industrial machinery maintenance.
The Role of Washers in Mechanical Systems
In mechanical systems, hardware washers play a crucial role in ensuring smooth operation and preventing damage. These simple yet vital components are designed to distribute the load evenly across surfaces, acting as a buffer between two or more parts. By providing a flat, stable surface, washers prevent the concentration of stress at any one point, which could lead to deformation, fatigue, or even failure. This is particularly important in applications where forces are significant, such as in engines, transmissions, and other heavy-duty machinery.
Washers also serve as a means of securing fasteners, like bolts and nuts, by providing additional friction and preventing slippage. They can accommodate misalignments between components, ensuring that mechanical systems function optimally even under less than ideal conditions. The variety of materials used in washers, from stainless steel to brass, makes them suitable for different environments and applications, making them an indispensable element in the world of mechanical engineering.
Uncovering the Significance of Inner Diameters
In the realm of engineering and manufacturing, understanding inner diameters is paramount, especially when it comes to hardware washers. These seemingly simple components play a crucial role in connecting and securing various parts within machinery and structures. Uncovering the significance of inner diameters involves recognizing their direct impact on structural integrity, load distribution, and overall performance.
By meticulously measuring and specifying inner diameters, engineers ensure that washers fit perfectly between bolts and plates. This precise alignment is vital for evenly distributing loads, preventing excessive stress concentration, and ensuring components don’t fail under pressure. In today’s sophisticated manufacturing landscape, where quality and reliability are paramount, paying meticulous attention to inner diameters – be it in the context of hardware washers or other mechanical parts – is a game-changer, fostering robust designs and enhancing overall system performance.
Types and Applications of Hardware Washers
Hardware washers are an essential component in various industries, offering a simple yet effective solution for fastening and sealing. These washers come in diverse types, each tailored to specific applications. For instance, spring washers, with their unique helical design, are ideal for securing fastenings in places where vibration is a factor, like automotive components or machinery. In contrast, lock washers provide a positive grip, preventing nut slippage in high-stress situations, commonly used in construction and mechanical engineering.
In the realm of precision assembly, plain washers act as a buffer between bolts and sensitive surfaces, ensuring even pressure distribution. They are ubiquitous in electronics manufacturing. Additionally, these washers play a crucial role in preventing corrosion and providing insulation in certain applications. The versatility of hardware washers makes them indispensable across industries, from automotive to electronics, contributing to the reliability and durability of various products.
Design Considerations for Optimal Performance
When designing inner diameters, especially for hardware washers, a thoughtful approach is essential to ensure optimal performance and longevity. Consideration should be given to the material selection, ensuring it aligns with the intended application’s requirements. For instance, in high-pressure washing systems, robust materials that can withstand intense forces without deformation are crucial. Additionally, the inner diameter’s geometry plays a vital role; smooth surfaces reduce friction, allowing for efficient fluid flow and minimizing wear over time.
For hardware washers, precise dimensions are key. Designing these inner diameters involves calculating specific clearances to accommodate various fastener sizes while maintaining structural integrity. Proper clearance ensures proper fastener seating and prevents damage during installation or removal processes, ultimately enhancing the washer’s performance in diverse mechanical settings.
Ensuring Safety and Reliability Through Washer Selection
When selecting hardware washers for any application, prioritizing safety and reliability is paramount. The right washer can prevent catastrophic failures by evenly distributing loads and managing dynamic forces. For instance, in industrial settings where high-pressure fluid systems are common, specific washer designs—like spiral or wave washers—can absorb misalignments and axial movement, ensuring components remain intact and preventing costly damage.
Moreover, choosing the appropriate hardware washer can extend equipment lifespan and minimize downtime. Corrosion-resistant materials like stainless steel are ideal for harsh environments, while specialized elastomers offer exceptional flexibility and dampening properties. By understanding these factors, users can make informed decisions, enhancing system performance and safety across various applications.
Hardware washers, with their diverse types and applications, play a critical role in mechanical systems by providing essential inner diameters. Understanding the significance of these dimensions ensures optimal performance and safety. By carefully considering design aspects and selecting appropriate washers, engineers can create reliable mechanisms that stand the test of time. In essence, hardware washers are not just components but integral parts that drive efficiency and longevity in various industries.