Maximizing Hardware Washer Lifespan: Strategies and Innovations for Fatigue Life
Hardware washers, vital components in machinery, vehicles, and construction, have a fatigue life aff…….
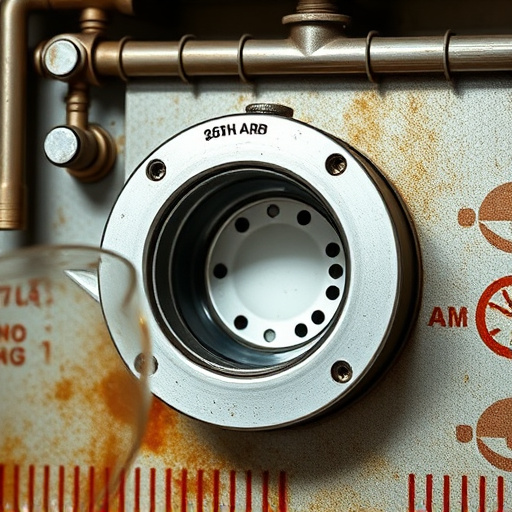
Hardware washers, vital components in machinery, vehicles, and construction, have a fatigue life affected by material composition, load patterns, environmental conditions, and design flaws. Engineers must optimize these factors for reliable performance and safety, using advanced materials like high-performance alloys or composites to enhance durability. Regular maintenance, including cleaning, inspection, and lubrication, extends washer lifespan while reducing operational costs and improving overall equipment effectiveness. Case studies demonstrate successful fatigue life optimization in diverse industries, setting new standards for hardware washers' durability and reliability.
“Hardware washers are critical components in industrial applications, facing relentless cyclical stress. Understanding fatigue life is crucial for maintaining operational efficiency and safety. This article delves into the intricacies of hardware washer fatigue, exploring its causes, from material properties to loading conditions. We discuss proven maintenance strategies and innovative design approaches that extend washer lifespan. Additionally, real-world case studies highlight successful fatigue life optimization techniques, emphasizing the impact of strategic choices on equipment reliability.”
- Understanding Fatigue Life: The Basics of Hardware Washers
- Factors Affecting Fatigue Life in Industrial Applications
- Maintenance Strategies to Prolong Hardware Washer Lifespan
- Advanced Materials and Design Innovations for Enhanced Durability
- Case Studies: Real-World Success Stories in Fatigue Life Optimization
Understanding Fatigue Life: The Basics of Hardware Washers
Fatigue life is a critical aspect of engineering and materials science, focusing on the longevity of materials under repetitive or cyclic loading. In the context of hardware washers, understanding fatigue life involves grasping how these components withstand repeated stress during their functional cycle. Hardware washers, often made from various metals or synthetic materials, experience significant strain as they distribute weight and maintain joint integrity in machinery, vehicles, and construction equipment.
The basic principle behind fatigue life is the cumulative effect of cyclic stresses below a material’s yield strength. Unlike static loading, which causes immediate failure, repetitive forces lead to gradual degradation over time. In hardware washers, this means that even modest stress cycles can, over months or years, result in cracks, deformities, or complete structural failure. Engineers and manufacturers must consider factors like material composition, load patterns, and environmental conditions to predict and optimize fatigue life, ensuring the reliability and safety of their designs.
Factors Affecting Fatigue Life in Industrial Applications
In industrial applications, several factors significantly influence fatigue life, particularly in critical components like hardware washers. One of the primary determinants is the material’s quality and properties; different metals and alloys exhibit varying resistance to fatigue failure due to their inherent strength and ductility. Another crucial aspect is the loading condition—the magnitude and frequency of forces acting on the washer determine its fatigue life. High-cycle fatigues, where components experience numerous stress cycles within a short period, demand careful consideration as they can lead to accelerated wear and tear compared to low-cycle fatigues.
Operational conditions play a significant role too. Environmental factors such as temperature extremes and exposure to corrosive substances can shorten the lifespan of hardware washers. Additionally, design intricacies like the presence of notches or surface imperfections act as stress concentrators, exacerbating fatigue cracks and reducing overall fatigue life. Understanding these factors is vital for engineers aiming to optimize washer designs and materials to enhance performance and safety in industrial settings.
Maintenance Strategies to Prolong Hardware Washer Lifespan
Proper maintenance is key to prolonging the lifespan of any machine, and hardware washers are no exception. Regular cleaning and inspection are essential strategies to keep these powerful tools in top condition. By regularly removing buildup and debris, users can prevent clogs and ensure optimal performance. Additionally, lubricating moving parts as recommended by the manufacturer reduces friction and wear, extending the washer’s life significantly.
Another effective approach is to establish a preventive maintenance schedule. This includes tracking usage, monitoring for unusual noises or vibrations, and addressing any issues promptly. Regular deep cleaning cycles with suitable detergents can remove accumulated residue, maintaining the efficiency of the hardware washer. These simple yet vital practices ensure that the equipment remains in excellent working order, maximizing its service life while delivering consistent results.
Advanced Materials and Design Innovations for Enhanced Durability
In the pursuit of extending fatigue life, advanced materials and design innovations play a pivotal role in enhancing durability across various applications. Modern engineering approaches, such as the strategic implementation of hardware washers, offer enhanced structural integrity and resilience against wear and tear. These components, crafted from high-performance alloys or composite materials, not only withstand extreme conditions but also significantly prolong the lifespan of machinery and equipment.
Through meticulous design considerations, engineers can optimize material distribution, stress concentration points, and corrosion resistance, all while minimizing weight. This convergence of enhanced materials and innovative designs translates into reduced maintenance frequency, lower operational costs, and increased safety margins in critical systems—a testament to the evolving capabilities in the realm of fatigue life enhancement.
Case Studies: Real-World Success Stories in Fatigue Life Optimization
In the realm of engineering and material science, case studies offer tangible examples of success stories that highlight the real-world applications of fatigue life optimization. One notable example involves the enhancement of hardware washers, essential components in various machinery. Through meticulous design refinements and advanced manufacturing techniques, engineers have significantly extended the service life of these washers, reducing failure rates and maintenance costs. This achievement underscores the power of implementing robust fatigue life analysis, incorporating innovative materials, and adopting smart design strategies.
Another inspiring case study focuses on the aerospace industry, where optimizing aircraft engine components has led to remarkable improvements in flight efficiency and safety. By studying fatigue behaviors and employing sophisticated modeling techniques, engineers have successfully designed lighter yet stronger parts, ultimately contributing to reduced fuel consumption and enhanced aviation performance. These success stories not only demonstrate the effectiveness of fatigue life optimization but also drive further innovations across diverse sectors, setting new benchmarks for durability and reliability.
Hardware washers play a critical role in industrial applications, with their fatigue life directly impacting overall equipment effectiveness. By understanding the basic principles and identifying factors influencing washerness longevity, manufacturers can implement effective maintenance strategies and adopt advanced materials to significantly enhance durability. Real-world case studies highlight the success of optimizing fatigue life, demonstrating that proactive approaches and innovative solutions are key to extending the service life of hardware washers in demanding environments.