Optimizing Hardware Washer Assembly: From Basics to Future Trends
Assembly sequence is critical for manufacturing high-quality hardware washers, involving strategic p…….
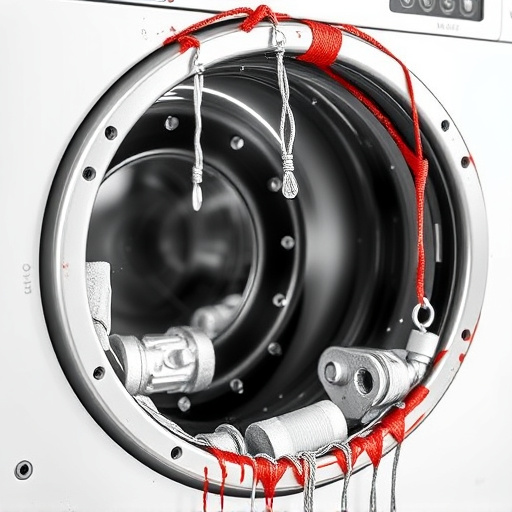
Assembly sequence is critical for manufacturing high-quality hardware washers, involving strategic part arrangement and coordination (drums, motors, water supply systems) for functionality, efficiency, and durability. This meticulous process streamlines production, minimizes errors, and aids troubleshooting/maintenance, ensuring reliable washers for diverse industrial applications. Key challenges include precise alignment and parts management, addressed through automated guidance systems, organized assembly lines, quality control checks, and regular training. The future of hardware washer assembly leans towards increased automation (robotics, CNC, AI) and sustainability (recyclable materials, energy efficiency).
In the realm of manufacturing, the assembly sequence plays a pivotal role in bringing hardware washers from raw materials to functional products. This comprehensive guide explores the intricacies of this process, underscoring its foundational importance for consistent quality and efficiency. From understanding the basic components to tackling common challenges, we delve into the art and science of assembling hardware washers. Additionally, we examine automation’s impact, quality control measures, and future trends shaping this critical manufacturing step.
- Understanding Assembly Sequence: A Foundation for Hardware Washers
- The Role of Assembly in Manufacturing Washer Components
- Step-by-Step Guide: Assemblage Process of a Hardware Washer
- Common Challenges and Solutions in Washer Assembly
- Automation vs. Manual Assembly: Benefits and Considerations for Hardware Washers
- Quality Control Measures During the Assembly Sequence
- Future Trends and Innovations in Hardware Washer Assembly Techniques
Understanding Assembly Sequence: A Foundation for Hardware Washers
Understanding Assembly Sequence is a fundamental step in the manufacturing process, especially for complex machinery like hardware washers. It refers to the systematic arrangement and coordination of parts to assemble a functional whole. In the context of hardware washers, this sequence involves precise steps to ensure the washer’s efficiency and durability. Each component, from the drum to the motor and water supply systems, must be meticulously fitted together, following a specific order.
This process is crucial in ensuring the optimal performance of hardware washers. A well-planned assembly sequence allows for seamless integration of parts, streamlining production and reducing potential errors. It also facilitates troubleshooting and maintenance, as technicians can follow a structured guide to disassemble and repair washers efficiently. Thus, a thorough understanding of this sequence is vital for manufacturers aiming to produce high-quality, reliable hardware washers.
The Role of Assembly in Manufacturing Washer Components
In the manufacturing process, assembly plays a pivotal role in producing hardware washers, ensuring their functionality and quality. The sequence involves carefully aligning and joining multiple parts to create a cohesive whole. This meticulous process demands precision and adherence to strict tolerances, especially in the case of small, intricate components like washers. Each step is crucial, from selecting the right materials to assembly techniques, as these directly impact the final product’s performance and longevity.
Assembly sequences for hardware washers typically commence with preparing the individual components, which may include metal sheets cut into specific shapes or pre-formed parts. These are then assembled using various methods such as threading, welding, or pressing, depending on design requirements. Skilled labor or advanced automation ensures each washer meets the necessary standards, guaranteeing its reliability in various applications across industries like automotive, construction, and machinery.
Step-by-Step Guide: Assemblage Process of a Hardware Washer
To assemble a hardware washer, follow this step-by-step guide. Begin by laying out all components on a clean workspace to ensure easy access and organization. Next, attach the wash drum to the motor shaft using the provided bolts and washers, making sure it’s securely fastened. Once that’s complete, connect the water supply lines according to the manufacturer’s instructions, ensuring proper sealing for leak-free operation.
Proceed by installing the agitator into the drum, aligning the components carefully. Then, attach the control panel and ensure all electrical connections are secure. Mount the lid on top, following the assembly directions, and verify that it opens and closes smoothly. Lastly, check all bolts and connections for tightness before powering on your hardware washer for the first time, ensuring a seamless cleaning experience ahead.
Common Challenges and Solutions in Washer Assembly
In the assembly sequence of hardware washers, several common challenges arise due to the intricate nature of these appliances. One of the primary hurdles is ensuring precise alignment during the installation of components like drums, motors, and transmission systems. Misalignment can lead to malfunction and noise, so robust alignment tools and well-trained assemblers are essential. Another challenge lies in managing the various parts, especially smaller components that are easily misplaced or damaged. Efficient inventory management systems and organized assembly lines help mitigate these issues.
Solutions involve adopting advanced assembly line techniques with automated guidance systems for accurate component placement. Additionally, implementing quality control checks at each stage of the assembly process ensures that only properly assembled washers progress to the next phase. Regular training sessions for workers on new technologies and best practices further enhance productivity and minimize errors. These strategies not only streamline the wash assembly process but also contribute to producing high-quality hardware washers that meet consumer expectations.
Automation vs. Manual Assembly: Benefits and Considerations for Hardware Washers
In the realm of hardware washing, the debate between automation and manual assembly is a significant one. Automation offers numerous advantages such as increased efficiency, reduced human error, and consistent quality. For instance, automated systems can precisely target and clean complex hardware components, ensuring no residue or contamination remains. This is especially crucial for industries where hygiene and precision are paramount, like medical device manufacturing. Moreover, automation enables round-the-clock operation, leading to faster production times and higher output capacities for hardware washer facilities.
However, manual assembly still has its merits. Human operators possess dexterity and fine motor skills that machines may struggle to replicate, especially when dealing with intricate or delicate parts. Manual handling also allows for more flexibility in adapting to unique or custom-designed hardware pieces. Additionally, human oversight is vital for quality control, as operators can visually inspect each component for any potential issues or defects that automated systems might miss. This blend of automation and manual expertise offers a compelling strategy for efficient and reliable hardware washing processes.
Quality Control Measures During the Assembly Sequence
During the assembly sequence, implementing robust quality control measures is paramount to ensure the final product meets stringent standards. This involves meticulous inspection at every stage, focusing on critical components like hardware washers. Specialized tools and trained personnel are employed to verify dimensions, identify defects, and ensure proper alignment, thereby guaranteeing both functionality and durability.
Regular audits and cross-referencing against design specifications further bolster quality assurance. Additionally, automated quality control systems, leveraging advanced sensors and imaging technology, play a crucial role in detecting even the subtlest anomalies, such as misaligned washers or debris intrusion. These measures collectively contribute to minimizing defects, enhancing product reliability, and fostering customer satisfaction.
Future Trends and Innovations in Hardware Washer Assembly Techniques
The future of hardware washer assembly techniques promises significant advancements, driven by the ever-evolving demands of the manufacturing industry. Innovations such as robotic automation and advanced computer numerical control (CNC) technologies are set to revolutionize assembly lines, enhancing precision and productivity. These technologies can handle intricate tasks with unmatched consistency, reducing human error and increasing efficiency. For instance, robots equipped with machine vision can accurately position and assemble components, ensuring each hardware washer meets the highest quality standards.
Additionally, the integration of artificial intelligence (AI) will enable predictive maintenance and smart quality control. AI algorithms can analyze assembly data to anticipate potential issues, allowing for proactive measures. This not only minimizes downtime but also enhances overall equipment effectiveness. As the industry leans towards more sustainable practices, we may see the rise of eco-friendly assembly techniques, utilizing recyclable materials and energy-efficient processes, further solidifying the importance of hardware washers in a greener manufacturing landscape.
The assembly sequence of hardware washers is a complex yet critical process that ensures these essential appliances function optimally. By understanding the fundamental aspects, from component manufacturing to quality control, manufacturers can streamline production and deliver high-quality products. The balance between automation and manual labor remains crucial, offering benefits such as increased efficiency and cost-effectiveness while requiring careful consideration of human error prevention. As technology advances, future trends in hardware washer assembly will likely involve innovative techniques that enhance precision, reduce downtime, and further improve overall product quality, solidifying their position as indispensable household items.