Optimizing Space: Guide to Hardware Washer Layouts
Optimizing the spacing of hardware washers is critical for their efficient operation, preventing dam…….
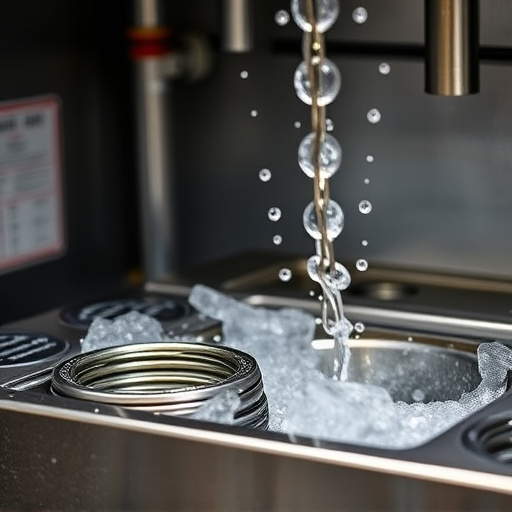
Optimizing the spacing of hardware washers is critical for their efficient operation, preventing damage and improving productivity. Factors include washer size, clearance for maintenance and ventilation, and strategic placement to avoid collisions. Following manufacturer guidelines on dimensions and weight capacities ensures optimal layout patterns like side-by-side installation. In industrial settings, proper spacing minimizes imbalances, noise, and inefficient water flow; while in retail, strategic positioning enhances customer experiences through streamlined queue management and improved product visibility.
In the realm of industrial cleaning, efficient spacing configuration for hardware washers is key to optimal performance and productivity. This article delves into the intricacies of understanding spacing requirements, exploring factors affecting washer placement, and offering best practices for precise arrangement. We also shed light on common mistakes to avoid and present compelling case studies showcasing successful implementations. Maximize your cleaning operations with this comprehensive guide tailored for hardware washers.
- Understanding Spacing Requirements for Hardware Washers
- Factors Affecting Spacing Between Washers
- Best Practices for Optimal Spacing Configuration
- Common Mistakes to Avoid in Spacing Hardware Washers
- Case Studies: Successful Spacing Implementations
Understanding Spacing Requirements for Hardware Washers
Understanding the spacing requirements for hardware washers is essential in ensuring efficient and safe operation. These machines, designed to clean industrial components, require careful consideration of space allocation both within the washer itself and the surrounding area. Proper spacing allows for unobstructed access, easy loading and unloading of parts, and adequate airflow to prevent overheating.
When setting up a hardware washer, it’s crucial to factor in the machine’s dimensions, including its length, width, and height, along with the space needed for maintenance and cleaning activities. Adequate clearances should be provided around the washer to facilitate movement of carts or conveyors used for part loading and unloading. Additionally, considering the proximity to walls and other equipment can prevent collisions and optimize workspace utilization.
Factors Affecting Spacing Between Washers
The spacing between hardware washers isn’t a one-size-fits-all affair; several factors come into play, dictating the optimal distance for efficient operation and space optimization. One key consideration is the type and size of the washers themselves. Larger machines require more breathing room to ensure proper airflow and prevent excessive heat buildup. Conversely, compact washers might fit snugly together without compromising performance.
Another significant factor is the layout of your laundry area. In a small space, minimizing the distance between washers can maximize capacity, but it’s crucial not to overcrowd. Conversely, ample space allows for better air circulation, which is beneficial for both energy efficiency and maintaining the longevity of your hardware washers.
Best Practices for Optimal Spacing Configuration
To achieve optimal spacing configuration for hardware washers, start by considering the manufacturer’s guidelines. Each washer has specific dimensions and weight capacities, so ensuring adequate space for proper ventilation and movement is crucial. A common best practice is to allow at least 1-2 inches of clearance around each unit to facilitate easy access, maintenance, and airflow.
Additionally, arranging hardware washers in a logical pattern can maximize efficiency. For example, positioning them side by side with a slight gap in between allows for a continuous workflow. This configuration not only maintains an uncluttered space but also ensures quick and hassle-free operation, which is especially beneficial in industrial settings where productivity is paramount.
Common Mistakes to Avoid in Spacing Hardware Washers
When installing or maintaining hardware washers, several common mistakes can lead to imbalances and potential damage. One of the most frequent errors is inadequate spacing between washers, which can cause them to spin unevenly, leading to noise and wear. It’s crucial to respect the recommended clearances for each specific washer model, as a uniform distribution ensures proper water flow and drainage. Ignoring these guidelines may result in blocked drains or inefficient operation.
Another mistake to avoid is cramming too many washers into a compact space. Overcrowding can obstruct the natural movement of water and air, promoting mold growth and creating an uneven wash surface. Always allow sufficient room for each washer to function optimally, ensuring both maintenance accessibility and efficient cleaning performance.
Case Studies: Successful Spacing Implementations
Successful spacing implementations in various settings offer valuable insights into creating optimal environments for different needs. For instance, consider a large-scale manufacturing facility employing numerous hardware washers. Efficient spacing here involves organizing machines to minimize travel time while maximizing production capacity. Well-planned aisles allow for smooth material and worker flow, enhancing productivity. Additionally, integrating storage solutions alongside these areas ensures quick access to essential supplies, further streamlining operations.
Another example is a retail store redesigning its layout to accommodate self-checkout stations and expanding product displays. Strategically placing these elements creates a seamless shopping experience, encouraging customer movement and interaction with products. This approach not only reduces congestion but also enhances sales opportunities by providing clear visibility of merchandise and facilitating efficient queue management at checkout areas.
In conclusion, understanding and adhering to optimal spacing requirements for hardware washers is paramount to ensuring efficient wash cycles, maximizing space utilization, and preventing damage. By considering factors like washer size, load capacity, and drainage needs, along with best practices and common mistakes to avoid, you can create a streamlined washing process. Successful implementations as showcased in case studies further emphasize the importance of thoughtful spacing configurations in any laundry or industrial setting.